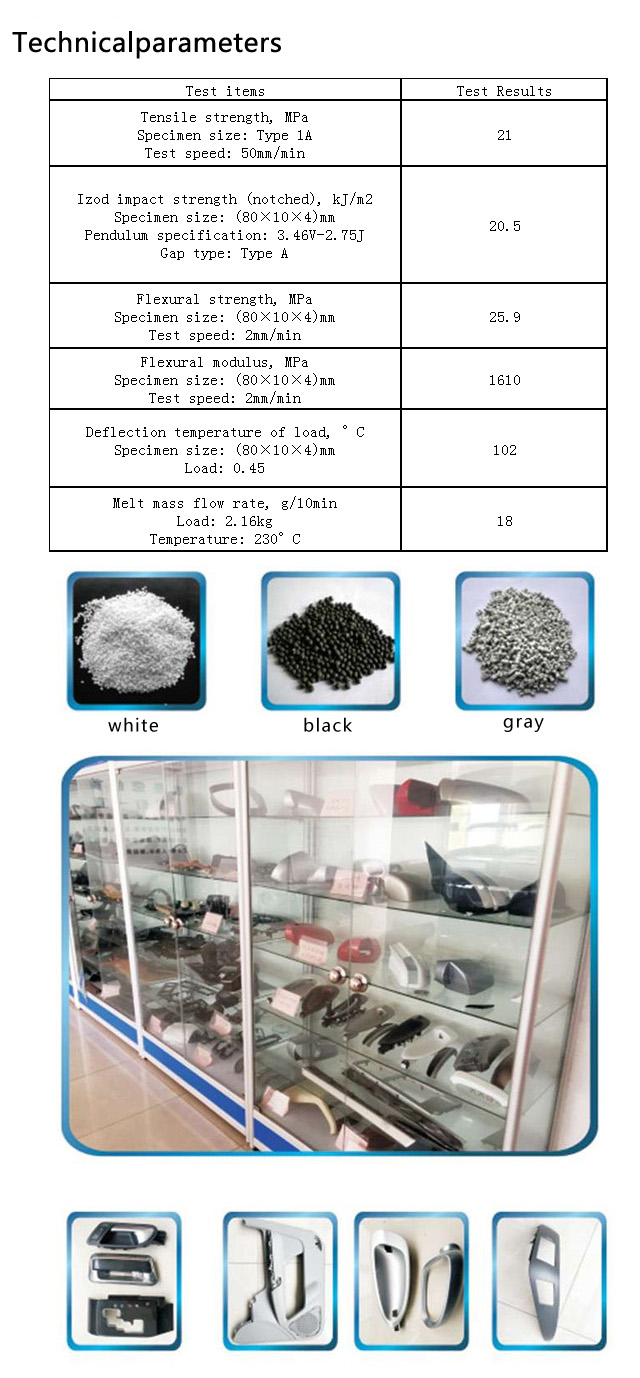

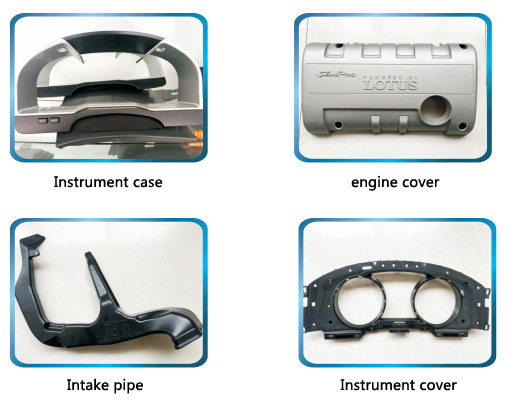
Injection molding analysis | |||
| Technology and equipment | Mold | material |
Weld Line | 1, injection pressure (speed) is too low or too high 2, back pressure setting is not suitable 3, tube temperature is too low | 1, the mold temperature is too low 2, the gate or runner is too small, the runner is too long 3, poor exhaust | 1, poor liquidity 2, the material is different material |
Silver grain | 1, barrel temperature is too high 2, screw speed is too fast 3, the nozzle is too small, too hot or blocked 4, the amount of plastic injection capacity of more than 80% of the machine 5, there is gas or water vapor in the melt 6, clear material is not complete | 1, the gate is too small 2, gate or runner blocked 3, mold surface micro-cracks | 1, the material did not fully dry 2, the material containing foreign body 3, the material pyrolysis |
Flash edge | 1, injection pressure (speed) is too high 2, Sol stay material tube time is too long 3, the molding cycle is too long 4, lack of lock mold 5, the material temperature is too high | 1, clamping surface contact bad 2, mold strength is not enough 3, poor exhaust 4, runner too long | 1, liquidity is good 2, too much lubricant |
Depression | 1, barrel or mold temperature is too high 2, injection pressure, speed is too low, the cycle is too short 3, packing pressure (time) is not enough 4, set the cooling time is not good 5, bad check valve | 1, gate or runner is too small 2, poor choice of gate location or type 3, pouring too early 4, tendons too thick 5, the flow is not balanced | 1, material mobility, shrinkage does not meet the requirements 2, the amount of material back too large |
Insufficient filling | 1, the amount of sol insufficient 2, barrel temperature is too low 3, back pressure set bad 4, injection pressure (speed) less than 5, the injection time is too short 6, check valve gap 7, the nozzle blocked | 1, the mold temperature is too low 2, the gate type or location of improper choice 3, bad exhaust mold 4, the mold of the runner (gate) is too small 5, the distribution of the mold cavity is not balanced | 1, the material itself is illiquid 2, poor material drying |
Flow marks | 1, barrel temperature is too low 2, injection pressure is too low 3, packing pressure (time) is not enough 4, the cycle time is not appropriate 5, Sol stay in the material pipe too long | 1, the mold temperature is too low 2, gate or runner is too small 3, poor exhaust | 1, material mobility requirements 2, improper lubricant 3, volatile too much |
bubble | 1, barrel temperature is too high 2, injection pressure, back pressure is too low 3, packing pressure (time) less than 4, the firing rate is too high 5, insufficient filling material 6, tube temperature setting bad district | 1, wall thickness (stiffeners) mold temperature is too high 2, poor gate or runner 3, poor choice of gate type or location 4, pouring too early 5, mold temperature is too low 6, poor exhaust | 1, material mobility, contractility does not meet the requirements 2, the amount of material back too much 3, the raw material is not fully dried |
Surface gloss | 1, barrel temperature is too low 2, insufficient shot pressure 3, nozzle temperature is low 4, sol in the tube time is too long 5, improper molding cycle | 1, poor mold finish 2, gate or runner is too small 3, the type or location of the wrong gate 4, bad exhaust 5, mold surface foreign body | 1, the material did not fully dry 2, improper mobility 3, the material itself is poor gloss |
Size difference | 1, unstable feeding 2, screw speed instability 3, the temperature out of control, back pressure instability 4, screw reset unstable 5, the molding cycle is unstable | 1, mold strength and lack of rigidity 2, using a bad form of a multi-cavity | 1, poor material drying, uneven particles 2, raw material shrinkage is too large 3, There are batches of material viscosity difference |
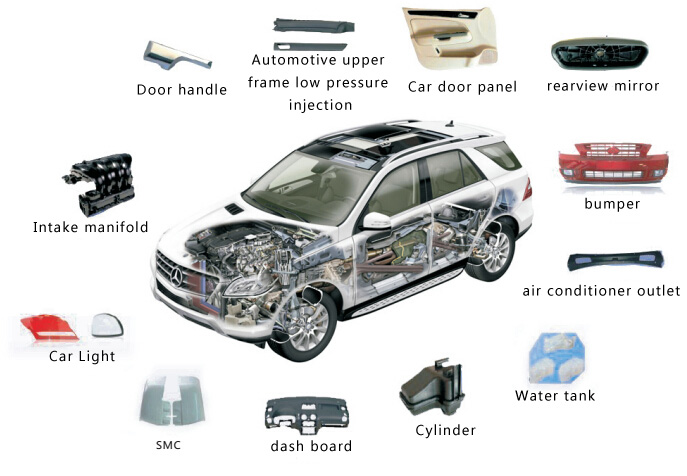